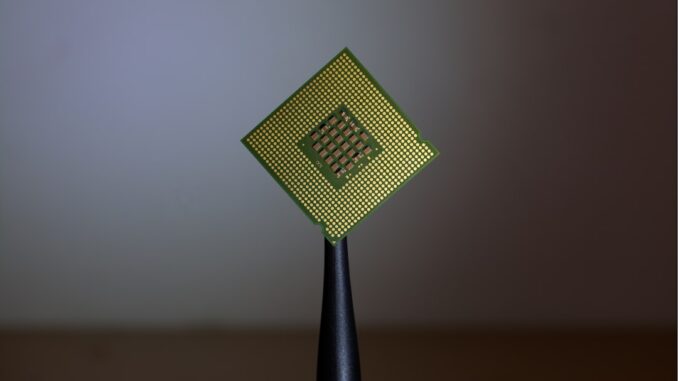
Integrated Circuits: Foundations, Evolution, and Global Impact
Many thanks to our sponsor Panxora who helped us prepare this research report.
Abstract
Integrated Circuits (ICs), often referred to as microchips or simply ‘chips’, stand as the bedrock of the modern digital age, fundamentally reshaping industries, societies, and daily life. Their unprecedented capacity for miniaturization, enhanced performance, and increased reliability has driven the technological revolution from the late 20th century to the present. This comprehensive research report meticulously traces the historical trajectory of IC development, from their conceptualization and independent invention to the relentless pursuit of ‘Moore’s Law’. It delves into the underlying semiconductor physics that enables their functionality, explores the diverse typologies of ICs, and provides an in-depth analysis of the intricate design and sophisticated fabrication processes. Furthermore, the report elucidates the pervasive and critical roles ICs play across an extensive array of industries, underscoring their indispensability in global innovation. A significant portion is dedicated to dissecting the highly complex and often precarious global supply chain of semiconductors, highlighting its inherent vulnerabilities to geopolitical shifts, economic pressures, and natural disruptions. Finally, the report addresses the escalating challenges associated with ensuring the security, authenticity, and trustworthiness of ICs, examining various threat vectors and the imperative for robust solutions, such as blockchain-enabled initiatives like ICtoken, to safeguard this foundational technology.
Many thanks to our sponsor Panxora who helped us prepare this research report.
1. Introduction
Integrated Circuits represent one of the most transformative inventions of the 20th century, profoundly altering the landscape of electronics and enabling a paradigm shift towards ubiquitous computing, instantaneous communication, and intelligent systems. From the humble beginnings of a few transistors on a single chip, ICs have evolved into extraordinarily complex ‘systems-on-chip’ (SoCs) containing billions of transistors, each performing intricate functions at nanosecond speeds. This relentless march of progress, often encapsulated by ‘Moore’s Law’ – the empirical observation that the number of transistors on a microchip doubles approximately every two years – has been the primary driver behind the exponential growth in computational power, data storage capacity, and network bandwidth.
The pervasiveness of ICs extends across virtually every facet of modern existence. They are the ‘brains’ within smartphones, personal computers, and servers that power the internet. They control the engines and safety systems in automobiles, facilitate advanced medical diagnostics and treatments, and enable the sophisticated weaponry and communication systems vital for national security. Beyond consumer gadgets, ICs are the invisible architects of industrial automation, smart cities, and critical infrastructure, underpinning global commerce and interconnectedness.
However, this deep integration and reliance on ICs have also introduced a new class of systemic vulnerabilities. The globalization of the semiconductor manufacturing ecosystem, while fostering efficiency and innovation, has inadvertently created a fragile and interdependent supply chain susceptible to geopolitical tensions, economic protectionism, natural disasters, and deliberate malicious interventions. Concerns regarding counterfeiting, intellectual property (IP) theft, hardware Trojans, and supply chain integrity have escalated, posing significant risks of device failure, data breaches, economic losses, and even national security threats. The ability to verify the authenticity and provenance of an IC throughout its lifecycle, from design to end-of-life, has become paramount.
This report seeks to provide a holistic and in-depth examination of Integrated Circuits. It commences with their historical genesis, tracing the pivotal innovations that paved their way. It then delves into the fundamental scientific principles underpinning their operation, categorizes their diverse types, and elaborates on the meticulously precise design and fabrication processes that bring them to life. A significant focus is placed on illustrating their indispensable role across a multitude of industries. Finally, the report critically assesses the intricate global supply chain, highlighting its inherent vulnerabilities and the pressing need for robust security measures and transparency initiatives, such as ICtoken, to ensure the continued integrity and reliability of this cornerstone technology.
Many thanks to our sponsor Panxora who helped us prepare this research report.
2. Historical Development of Integrated Circuits
The conceptualization and realization of the Integrated Circuit marked a revolutionary leap from the era of discrete electronic components, which had inherent limitations in terms of size, reliability, and manufacturing complexity. Prior to ICs, electronic devices relied on vacuum tubes, which were bulky, consumed significant power, generated considerable heat, and were prone to failure. The invention of the transistor at Bell Labs in 1947 by John Bardeen, Walter Brattain, and William Shockley offered a solid-state alternative, promising miniaturization and improved reliability. However, even with transistors, circuits comprised individual components soldered together, leading to complex wiring, bulky designs for advanced systems, and susceptibility to failure points at each solder joint.
The urgent need for more compact, reliable, and cost-effective electronic systems, particularly for missile guidance and space exploration programs, spurred the race for integration. Two individuals, working independently and almost simultaneously, are credited with the invention of the Integrated Circuit:
-
Jack Kilby (Texas Instruments, 1958): Kilby’s breakthrough came during a summer sabbatical when he realized that all components of a circuit – resistors, capacitors, and transistors – could be formed from a single block of semiconductor material, specifically germanium. His prototype, demonstrated on 12 September 1958, was a phase-shift oscillator consisting of a transistor, three resistors, and a capacitor, all integrated onto a single piece of germanium substrate. While rudimentary, it proved the feasibility of a monolithic circuit. Kilby’s approach involved connecting the individual components on the block with fine gold wires.
-
Robert Noyce (Fairchild Semiconductor, 1959): Noyce, building upon the planar process developed by Jean Hoerni at Fairchild Semiconductor, conceived a more practical and manufacturable approach. The planar process allowed for the diffusion of impurities into the silicon wafer through patterned oxide layers, creating the active and passive components on one side of the wafer. Crucially, Noyce’s innovation involved depositing a thin layer of metal (aluminum) on top of the silicon oxide to interconnect the components directly on the chip, eliminating the need for external wires. This ‘monolithic’ approach, utilizing silicon, offered superior insulation between components and was inherently more scalable for mass production. Noyce filed his patent application just a few months after Kilby’s demonstration, on 30 July 1959.
While Kilby demonstrated the first functional integrated circuit, Noyce’s planar process provided the blueprint for scalable and cost-effective mass production, which became the cornerstone of the modern semiconductor industry. Both inventors received the U.S. patent for the integrated circuit, highlighting their complementary contributions.
2.1. The Era of Integration and Moore’s Law
The 1960s witnessed the nascent commercialization of ICs. Early applications included hearing aids and military systems. The Apollo Guidance Computer, developed by MIT Instrumentation Laboratory in the mid-1960s, was one of the first major consumers of ICs, utilizing thousands of integrated logic gates to control the Apollo spacecraft, demonstrating their reliability in extreme conditions.
In 1965, Gordon Moore, then director of research and development at Fairchild Semiconductor, made an observation that would become a guiding principle for the industry: the number of components (primarily transistors) on an integrated circuit for minimum cost per component had approximately doubled every year. Later revised to every two years, this observation became known as ‘Moore’s Law’. While not a physical law, it has served as an aspirational goal and a self-fulfilling prophecy, driving innovation in design, materials science, and fabrication techniques.
This relentless pursuit of miniaturization and increased density led to several stages of integration:
- Small-Scale Integration (SSI) (early 1960s): Up to 100 transistors per chip, typically containing a few logic gates or flip-flops.
- Medium-Scale Integration (MSI) (late 1960s): From 100 to 1,000 transistors, encompassing more complex functions like decoders, adders, and counters.
- Large-Scale Integration (LSI) (1970s): From 1,000 to 10,000 transistors, enabling the development of early microprocessors (e.g., Intel 4004 in 1971, the first commercial microprocessor) and memory chips.
- Very-Large-Scale Integration (VLSI) (1980s): Over 10,000 transistors, leading to the creation of more powerful microprocessors (e.g., Intel 80386), dynamic random-access memory (DRAM) chips with megabits of storage, and complex application-specific integrated circuits (ASICs). This era truly democratized computing.
- Ultra-Large-Scale Integration (ULSI) (1990s): Millions of transistors, facilitating the development of sophisticated microprocessors for personal computers and advanced graphics processors.
- Gigascale Integration (GSI) (2000s onwards): Billions of transistors, leading to multi-core processors, System-on-Chips (SoCs), and the advanced memory architectures found in today’s high-performance computing and mobile devices. Modern processors can contain tens of billions of transistors (e.g., Apple’s M3 Max chip boasts 92 billion transistors).
The evolution of ICs has not only been about increasing transistor count but also about improving performance (speed, power efficiency), reducing cost per function, and integrating diverse functionalities onto a single die. This continuous innovation has been fueled by advancements in materials science, lithography, etching, and sophisticated Electronic Design Automation (EDA) tools.
Many thanks to our sponsor Panxora who helped us prepare this research report.
3. Fundamental Principles of Semiconductor Physics
To comprehend how Integrated Circuits function, it’s essential to grasp the basic principles of semiconductor physics upon which they are built. Semiconductors are materials that have electrical conductivity between that of a conductor (like copper) and an insulator (like glass). Their unique property lies in their ability to control this conductivity by introducing small amounts of impurities or by applying electric fields.
3.1. Silicon as the Cornerstone Material
Silicon (Si) is the dominant semiconductor material for IC fabrication due to its abundance, excellent electrical properties (particularly its ability to form a stable native oxide, SiO2, which is an excellent insulator), and mature processing techniques. Pure silicon is an intrinsic semiconductor, meaning its electrical conductivity is very low at room temperature. Its atoms form a crystal lattice, with each silicon atom sharing its four valence electrons with four neighboring atoms, forming strong covalent bonds.
3.2. Doping: Tailoring Conductivity
The conductivity of silicon is precisely controlled through a process called ‘doping’, where small amounts of specific impurities (dopants) are introduced into the crystal lattice. This creates two types of extrinsic semiconductors:
- N-type (Negative-type) Silicon: Created by introducing pentavalent impurities (elements with five valence electrons, like Phosphorus (P) or Arsenic (As)). These dopants replace silicon atoms in the lattice, and their fifth valence electron is loosely bound, becoming a ‘free electron’ available for conduction. Electrons are the majority charge carriers.
- P-type (Positive-type) Silicon: Created by introducing trivalent impurities (elements with three valence electrons, like Boron (B)). These dopants create a ‘hole’ (a missing electron) in the covalent bond structure. Holes behave as positive charge carriers and are the majority carriers.
3.3. The PN Junction
The fundamental building block of most semiconductor devices, including transistors, is the ‘PN junction’. This is formed when p-type and n-type silicon are brought into intimate contact. At the junction, electrons from the n-side diffuse into the p-side, and holes from the p-side diffuse into the n-side. This diffusion creates a ‘depletion region’ around the junction, devoid of free charge carriers, and establishes a built-in electric field that opposes further diffusion.
- Forward Bias: Applying a positive voltage to the p-side and a negative voltage to the n-side reduces the depletion region, allowing current to flow easily across the junction.
- Reverse Bias: Applying a positive voltage to the n-side and a negative voltage to the p-side widens the depletion region, effectively blocking current flow (except for a very small leakage current).
The PN junction acts as a diode, allowing current to flow predominantly in one direction.
3.4. Transistors: The Electronic Switches
Transistors are the core active components of ICs, acting as electronic switches or amplifiers. The most common type in modern ICs is the ‘Metal-Oxide-Semiconductor Field-Effect Transistor (MOSFET)’. A MOSFET has three primary terminals:
- Gate (G): A metal (or polysilicon) electrode insulated from the semiconductor by a thin oxide layer.
- Source (S): A heavily doped region.
- Drain (D): Another heavily doped region.
The MOSFET operates by applying a voltage to the gate, which creates an electric field that modulates the conductivity of a channel between the source and drain. In a typical ‘enhancement-mode n-channel MOSFET’:
- When no voltage is applied to the gate, the channel is non-conductive.
- When a sufficient positive voltage is applied to the gate, it attracts electrons from the source and drain regions into the channel, effectively creating an n-type conductive path. This allows current to flow from the drain to the source, essentially turning the switch ‘on’.
By carefully arranging and interconnecting billions of these tiny MOSFETs, complex logic functions, memory cells, and analog circuits can be realized on a single chip. The ability to precisely control the doping, oxide thickness, and dimensions of these structures is what makes IC fabrication an extremely challenging and precise endeavor.
Many thanks to our sponsor Panxora who helped us prepare this research report.
4. Types of Integrated Circuits
Integrated Circuits are incredibly diverse, each category meticulously designed to perform specific functions within an electronic system. Their classification often depends on the nature of the signals they process, their level of programmability, or their primary application.
4.1. Analog ICs
Analog ICs are designed to process continuous signals, such as voltage, current, temperature, or sound, which vary smoothly over time. They are crucial for interfacing with the real world, which is inherently analog. Key characteristics include high precision, low noise, and the ability to handle a wide range of frequencies.
- Operational Amplifiers (Op-Amps): Versatile building blocks used for amplification, filtering, summing, and differentiation. They are found in audio equipment, medical instruments, and industrial control systems.
- Voltage Regulators: Maintain a constant output voltage despite fluctuations in input voltage or load current. Essential for stable power supplies in all electronic devices.
- Audio Amplifiers: Boost audio signals for speakers or headphones, ensuring clear sound reproduction.
- Radio Frequency (RF) ICs: Process high-frequency signals for wireless communication (e.g., transceivers in mobile phones, Wi-Fi modules, GPS receivers).
- Sensors and Actuators (Interfacing): While sensors themselves might not be ICs (e.g., thermistors), analog ICs are vital for conditioning the analog signals they produce before conversion to digital.
4.2. Digital ICs
Digital ICs process discrete signals, typically represented as binary values (0s and 1s). They are the backbone of all computing and digital control systems, enabling logical operations, data storage, and processing. Their primary advantage lies in their robustness against noise and their ease of replication.
- Microprocessors (CPUs): The ‘brains’ of computers and smart devices. They execute instructions, perform arithmetic and logical operations, and manage data flow. Modern CPUs are highly complex, featuring multiple processing cores, large on-chip caches, and specialized instruction sets for various tasks.
- Microcontrollers (MCUs): Smaller, self-contained computing systems on a single chip, integrating a CPU, memory (RAM, ROM, Flash), and peripheral interfaces (e.g., ADCs, timers, GPIOs). They are optimized for embedded applications where specific tasks need to be performed with low power consumption and cost-effectiveness (e.g., in washing machines, remote controls, IoT devices).
- Memory ICs: Store digital data.
- RAM (Random Access Memory): Volatile memory used for temporary data storage while a device is active.
- SRAM (Static RAM): Faster, consumes more power, and holds data as long as power is supplied. Used for caches (CPU, GPU).
- DRAM (Dynamic RAM): Slower, consumes less power, requires periodic refreshing. Used as main system memory (RAM in PCs, smartphones).
- ROM (Read-Only Memory): Non-volatile memory that retains data even without power.
- EEPROM (Electrically Erasable Programmable ROM): Can be electrically erased and reprogrammed multiple times. Used for storing configuration data.
- Flash Memory: A type of EEPROM, widely used for data storage in SSDs, USB drives, smartphones, and cameras due to its high density, speed, and non-volatility.
- RAM (Random Access Memory): Volatile memory used for temporary data storage while a device is active.
- Logic ICs: Perform fundamental Boolean logic operations (AND, OR, NOT, XOR). These include:
- Standard Logic Gates: Basic building blocks in digital circuits.
- Application-Specific Integrated Circuits (ASICs): Custom-designed ICs for a specific application. They offer high performance, low power, and small size for that specific task but are expensive to design and have long lead times. Examples include chips in smartphones, network routers, and cryptocurrency miners.
- Field-Programmable Gate Arrays (FPGAs): Reconfigurable digital ICs whose logic gates and interconnects can be programmed by the user after manufacturing. They offer flexibility and faster time-to-market than ASICs, suitable for prototyping, low-volume production, and applications requiring hardware reconfigurability (e.g., data centers, aerospace, telecommunications).
- Digital Signal Processors (DSPs): Specialized microprocessors optimized for performing rapid, repetitive mathematical operations on digital signals (e.g., filtering, FFTs). Found in audio/video processing, telecommunications, and medical imaging.
4.3. Mixed-Signal ICs
Mixed-Signal ICs integrate both analog and digital functionalities on a single chip. They serve as crucial bridges between the analog real world and the digital domain, enabling systems to interpret and act upon physical phenomena.
- Analog-to-Digital Converters (ADCs): Convert continuous analog signals into discrete digital representations.
- Digital-to-Analog Converters (DACs): Convert digital signals back into continuous analog signals.
- Communication ICs: Many communication chips (e.g., for Bluetooth, Wi-Fi, Ethernet) are mixed-signal, handling both analog radio frequencies and digital data processing.
- Power Management ICs (PMICs): While related to power ICs, many PMICs integrate digital control logic with analog power conversion circuits to efficiently manage power distribution in complex systems like smartphones.
4.4. Power ICs
Power ICs are specifically designed to manage, convert, and regulate electrical power within electronic systems. They handle higher voltages and currents than typical signal processing ICs and are essential for energy efficiency and system stability.
- Voltage Regulators (Switching and Linear): Efficiently convert and stabilize supply voltages for various components.
- Battery Management Systems (BMS) ICs: Monitor and control the charging, discharging, and health of battery packs, especially critical in electric vehicles and portable devices.
- Motor Drivers: Control the speed and direction of electric motors in various applications from industrial robots to drones.
- LED Drivers: Regulate current to Light Emitting Diodes for consistent brightness and extended lifespan.
Each of these IC types contributes synergistically to the complex functionality of modern electronic devices, demonstrating the remarkable versatility and specialization within the semiconductor industry.
Many thanks to our sponsor Panxora who helped us prepare this research report.
5. Design and Fabrication Processes
The creation of an Integrated Circuit is an extraordinarily complex, multi-stage process that combines highly sophisticated engineering, material science, and precision manufacturing. It can be broadly divided into the design phase and the fabrication (or manufacturing) phase.
5.1. The Design Phase: From Concept to Blueprint
The design of an IC begins with a conceptual idea and culminates in a detailed set of masks used in the fabrication process. This phase is heavily reliant on highly specialized Electronic Design Automation (EDA) software tools.
-
System-Level Design and Architecture Definition: At the highest level, engineers define the IC’s overall functionality, performance requirements (speed, power consumption), interfaces, and target applications. This involves breaking down the system into major functional blocks (e.g., CPU, memory controller, I/O peripherals).
-
RTL (Register-Transfer Level) Design: The system’s behavior is described using Hardware Description Languages (HDLs) like Verilog or VHDL. This high-level description specifies how data moves between hardware registers and how logical operations are performed. Extensive simulation and verification are performed at this stage to ensure the design’s correctness.
-
Logic Synthesis: The HDL code is translated into a gate-level netlist, which is a description of the circuit using standard logic gates (AND, OR, NOT) from a pre-characterized library. EDA tools perform optimizations to meet performance, power, and area constraints.
-
Physical Design (Layout):
- Floorplanning: Major functional blocks are arranged on the chip to optimize for area, minimize interconnections, and facilitate power distribution.
- Place and Route: Individual logic gates and memory cells are placed onto the silicon substrate, and then electrical connections (wires) are routed between them. This is a highly complex optimization problem, aiming for minimal wire length, avoiding crosstalk, and ensuring timing closure.
- Design Rule Checking (DRC): Automated tools rigorously check the layout against foundry-specific rules (e.g., minimum wire width, spacing) to ensure manufacturability.
- Layout Versus Schematic (LVS): Verifies that the physical layout accurately represents the original circuit schematic.
- Post-Layout Simulation: The routed design is re-simulated, incorporating parasitic effects (resistance, capacitance) from the physical layout, to ensure performance targets are still met.
-
Mask Generation: Once the physical design is finalized and verified, it is converted into a series of photomasks. Each mask corresponds to a specific layer of the IC (e.g., diffusion, polysilicon, metal layers) and defines the patterns to be transferred onto the silicon wafer during fabrication. These masks are incredibly precise, often created using electron-beam lithography.
5.2. The Fabrication Phase: Bringing the Design to Life
IC fabrication, also known as ‘wafer fabrication’ or ‘wafer fab’, is an incredibly precise and repetitive process performed in ultra-clean environments (cleanrooms) to prevent contamination, which can cause defects and render chips non-functional. It involves building up the circuit layer by layer on a thin wafer of pure silicon.
-
Wafer Preparation: Starts with high-purity silicon ingots (boules) grown from molten silicon. These ingots are then sliced into thin, highly polished wafers, typically 200mm or 300mm in diameter, serving as the substrate for hundreds or thousands of identical ICs.
-
Oxidation: A thin layer of silicon dioxide (SiO2) is grown on the wafer surface, usually by exposing the silicon to oxygen at high temperatures (thermal oxidation). This layer serves as an electrical insulator, a protective coating, and a mask for subsequent diffusion or implantation steps.
-
Photolithography (Pattern Transfer): This is the most critical step for defining circuit features. It involves:
- Photoresist Application: The wafer is coated with a light-sensitive polymer called photoresist.
- Exposure: A photomask, containing the pattern for a specific layer, is placed over the wafer. Ultraviolet (UV) light (or Deep UV, Extreme UV for advanced nodes) is shone through the mask, exposing selective areas of the photoresist. Depending on the photoresist type, exposed or unexposed areas become soluble.
- Development: A chemical developer selectively removes either the exposed or unexposed photoresist, creating a patterned resist layer that mirrors the mask design.
-
Etching: The patterned photoresist acts as a stencil. Exposed areas of the underlying material (e.g., silicon dioxide, polysilicon, metal) are then removed through etching. This can be:
- Wet Etching: Using liquid chemicals, which is often isotropic (etches equally in all directions).
- Dry Etching (Plasma Etching): Using chemically reactive plasmas, which offers anisotropic etching (etches primarily in one direction), crucial for creating fine, vertical features.
Once etching is complete, the remaining photoresist is stripped away.
-
Doping (Ion Implantation or Diffusion): Impurities (dopants like boron or phosphorus) are introduced into specific regions of the silicon to create p-type and n-type areas, forming transistors and resistors. Ion implantation precisely controls the depth and concentration of dopants by accelerating ions towards the wafer. Diffusion involves exposing the wafer to a gas containing dopants at high temperatures.
-
Deposition: Thin layers of various materials are deposited onto the wafer. Common methods include:
- Chemical Vapor Deposition (CVD): Reactant gases flow over the wafer, decomposing and depositing a thin solid film (e.g., polysilicon, silicon dioxide, silicon nitride).
- Physical Vapor Deposition (PVD) / Sputtering: Atoms are ejected from a target material by bombardment with ions and then deposited onto the wafer (e.g., for metal layers).
-
Metallization (Interconnects): Multiple layers of conductive material (historically aluminum, now predominantly copper for advanced nodes due to its lower resistance) are deposited and patterned to form the electrical connections between transistors and other components. Vias (vertical connections) are created to link different metal layers.
-
Chemical Mechanical Planarization (CMP): After each deposition and patterning step, the wafer surface can become uneven. CMP uses a combination of chemical slurry and mechanical polishing to achieve a perfectly flat surface before the next layer is added. This is crucial for maintaining focus and resolution in subsequent photolithography steps.
These steps are repeated dozens of times, layer by layer, to build up the complex three-dimensional structure of an Integrated Circuit. A typical advanced IC can have 15-20 photolithography steps and over 100 processing steps in total.
5.3. Post-Fabrication Processes
Once fabrication is complete, the wafers undergo further processing:
-
Wafer Testing (Probe Testing): Each individual IC (die) on the wafer is tested using probes to identify defective chips. Defective dies are marked (e.g., with ink).
-
Dicing: The wafer is cut into individual dies using a high-precision saw.
-
Packaging: Each good die is mounted into a protective package (e.g., DIP, QFN, BGA, CSP). The package provides mechanical protection, heat dissipation, and electrical connections to the outside world through pins or solder balls. Wire bonding or flip-chip technology connects the die pads to the package leads.
-
Final Testing: The packaged ICs undergo thorough final electrical and functional testing to ensure they meet specifications before being shipped to customers.
This entire process, from design to packaged chip, can take several months and requires massive capital investment in fabrication facilities (fabs) and highly skilled labor.
Many thanks to our sponsor Panxora who helped us prepare this research report.
6. Role of Integrated Circuits Across Industries
The transformative power of Integrated Circuits lies in their ability to imbue devices and systems with unprecedented levels of intelligence, efficiency, and functionality. Their impact spans virtually every modern industry, acting as a critical enabler for innovation and progress.
6.1. Consumer Electronics
ICs are the invisible workhorses behind the vast array of consumer electronics that define daily life. They enable the miniaturization, processing power, and battery life that users demand.
- Smartphones and Tablets: At their core, these devices are sophisticated System-on-Chips (SoCs) integrating multi-core CPUs, powerful GPUs, memory controllers, digital signal processors, image signal processors, and various connectivity modules (Wi-Fi, Bluetooth, 5G modems). They power operating systems, high-resolution displays, advanced cameras, and countless applications.
- Wearable Devices: Smartwatches, fitness trackers, and hearables rely on ultra-low-power MCUs, specialized sensors, and compact RFICs for health monitoring, connectivity, and gesture recognition.
- Smart Home Devices: From smart thermostats and lighting systems to security cameras and voice assistants, ICs enable connectivity (Wi-Fi, Zigbee, Z-Wave), sensor data processing, and local AI inference.
- Gaming Consoles and PCs: High-performance CPUs, GPUs (graphics processing units), and specialized memory controllers are essential for rendering complex graphics, physics simulations, and immersive gaming experiences.
- Home Appliances: Modern washing machines, refrigerators, and ovens utilize microcontrollers for precise control, energy management, and smart connectivity features.
6.2. Automotive Industry
The automotive sector has undergone a profound transformation driven by electronics, with ICs at the forefront. Modern vehicles are essentially ‘computers on wheels’, relying heavily on semiconductors for safety, performance, connectivity, and autonomy.
- Engine Control Units (ECUs): Sophisticated microcontrollers and DSPs manage fuel injection, ignition timing, and emission control for optimal performance and fuel efficiency.
- Safety Systems: ICs power Anti-lock Braking Systems (ABS), Electronic Stability Control (ESC), airbags, and increasingly, Advanced Driver-Assistance Systems (ADAS). ADAS relies on powerful vision processors, radar/lidar ICs, and sensor fusion units to enable features like adaptive cruise control, lane-keeping assist, and automatic emergency braking.
- Infotainment Systems: High-performance SoCs drive navigation, multimedia playback, connectivity (Apple CarPlay, Android Auto), and dashboard displays.
- Electric Vehicles (EVs): Power ICs, Battery Management System (BMS) ICs, and motor control ICs are fundamental for managing the high voltage battery pack, optimizing energy flow, and controlling electric motors.
- Autonomous Driving: This represents the pinnacle of automotive IC integration, requiring extremely powerful AI accelerators (GPUs, NPUs), high-speed networking chips, and robust safety-critical processors to interpret sensor data, make real-time decisions, and control vehicle movements.
6.3. Defense and Aerospace
Reliability, performance, and security are paramount in defense and aerospace applications, where ICs are critical for mission success and national security.
- Avionics: Flight control systems, navigation units (GPS/INS), radar systems, and communication equipment in aircraft and spacecraft depend on robust, often radiation-hardened, ICs.
- Missile Guidance and Control: DSPs and specialized processors provide real-time control and target tracking for precision weaponry.
- Secure Communications: Cryptographic ICs and secure processors are used in military communication systems to ensure data integrity and confidentiality.
- Satellites and Space Exploration: ICs must withstand extreme temperatures, radiation, and vacuum conditions, enabling communication, data processing, and scientific instrumentation in orbit and beyond.
6.4. Medical and Healthcare
ICs are revolutionizing healthcare by enabling more accurate diagnostics, personalized treatments, and advanced patient care.
- Diagnostic Equipment: ICs are integral to MRI scanners, CT scanners, ultrasound machines, and X-ray systems, facilitating data acquisition, image processing, and display.
- Patient Monitoring Systems: Wearable sensors and bedside monitors use low-power MCUs and analog front-ends to continuously track vital signs, glucose levels, and cardiac activity.
- Implantable Devices: Pacemakers, cochlear implants, and neural interfaces rely on ultra-low-power, biocompatible ICs for long-term operation within the human body.
- Surgical Robotics: High-performance processors and motor control ICs enable precise movements and real-time feedback for minimally invasive surgeries.
- Point-of-Care Devices: Portable diagnostic tools often incorporate specialized ICs for rapid and on-site analysis of biological samples.
6.5. Industrial Automation and Manufacturing
The rise of Industry 4.0 and smart factories is fundamentally powered by ICs, driving efficiency, precision, and connectivity in industrial environments.
- Programmable Logic Controllers (PLCs): MCUs and DSPs are core to PLCs, which control and automate industrial processes and machinery (e.g., assembly lines, robotics).
- Robotics: Industrial robots utilize powerful microprocessors, motor drivers, and sensor interface ICs for complex movements, vision systems, and collaborative tasks.
- Process Control Systems: ICs are crucial in distributed control systems (DCS) for managing complex chemical plants, power grids, and water treatment facilities, ensuring real-time monitoring and control.
- IoT for Industrial Applications (IIoT): Low-power wireless ICs and edge processors enable sensors and actuators to collect and transmit data from machinery, facilitating predictive maintenance and operational optimization.
6.6. Telecommunications and Data Centers
ICs are the backbone of global communication networks and the digital infrastructure that underpins the internet.
- 5G Infrastructure: Massive MIMO (Multiple-Input Multiple-Output) antenna systems, base stations, and core network equipment rely on high-frequency RFICs, powerful DSPs, and custom ASICs to handle immense data traffic and low latency requirements.
- Optical Networks: Optical transceivers, switches, and routers utilize specialized ICs for high-speed data transmission over fiber optic cables.
- Data Centers: Server farms are packed with high-performance CPUs, large-capacity memory chips, network interface controllers (NICs), and specialized accelerators (GPUs, ASICs) for cloud computing, AI training, and data storage.
- Edge Computing: Lower-power, but still powerful, ICs are deployed closer to data sources to reduce latency and bandwidth demands.
The ubiquity of ICs underscores their indispensable role in propelling technological advancement and shaping the future across every sector of the global economy.
Many thanks to our sponsor Panxora who helped us prepare this research report.
7. Global Supply Chain and Vulnerabilities
The semiconductor supply chain is arguably the most complex and globalized manufacturing ecosystem on the planet. It is a multi-tiered, interconnected network spanning raw material extraction, sophisticated design, highly capital-intensive fabrication, assembly, testing, and distribution. This global specialization has fostered efficiency and innovation, but it also creates profound interdependencies and inherent vulnerabilities.
7.1. Mapping the Multi-Stage Supply Chain
The semiconductor supply chain involves distinct stages, often dominated by different regions or companies:
-
Raw Materials: The process begins with ultra-pure silicon, sourced primarily from sand (silica). Key suppliers of polysilicon and silicon wafers include Japan (Shin-Etsu Chemical, Sumco), Germany (Wacker Chemie), and the US (Hemlock Semiconductor). Other critical materials like photoresists, specialty chemicals, and rare gases are also sourced globally, often with highly concentrated production in a few specialized companies (e.g., Japan for photoresists and some noble gases).
-
Electronic Design Automation (EDA) Software and IP Cores: The highly specialized software tools used for IC design (synthesis, simulation, layout, verification) are dominated by a handful of US companies (Synopsys, Cadence, Siemens EDA, formerly Mentor Graphics). Essential intellectual property (IP) blocks, such as CPU architectures (e.g., ARM Holdings from the UK), specialized memory controllers, and communication interfaces, are licensed from design companies or third-party IP vendors.
-
Manufacturing Equipment: The fabrication of ICs requires highly advanced and precise machinery. This sector is dominated by companies from the US, Japan, and the Netherlands:
- Lithography: ASML (Netherlands) is the near-monopoly supplier of cutting-edge Extreme Ultraviolet (EUV) lithography systems, essential for manufacturing chips at 7nm nodes and below. Nikon and Canon (Japan) provide DUV lithography.
- Deposition and Etching: Applied Materials (US), Lam Research (US), Tokyo Electron (Japan).
- Metrology and Inspection: KLA Corporation (US).
-
Integrated Device Manufacturers (IDMs): Companies that design, fabricate, and package their own chips (e.g., Intel, Samsung, Micron, Texas Instruments). They own and operate their own foundries.
-
Fabless Design Houses: Companies that design ICs but outsource their fabrication to specialized foundries (e.g., Apple, Qualcomm, NVIDIA, AMD, Broadcom). This model allows them to focus solely on design and innovation without the immense capital expenditure of running a fab.
-
Foundries (Pure-Play Fabricators): Companies that exclusively manufacture chips designed by fabless companies. This segment is highly concentrated and strategically vital:
- TSMC (Taiwan Semiconductor Manufacturing Company): The world’s largest and most technologically advanced foundry, producing chips for a vast array of global companies, including Apple, Qualcomm, and NVIDIA. It is the leading manufacturer of chips at the most advanced process nodes (e.g., 5nm, 3nm).
- Samsung Foundry (South Korea): A major competitor to TSMC, also at the leading edge of technology nodes, serving both its internal needs and external fabless clients.
- GlobalFoundries (US/Singapore/Germany): Specializes in mature and specialized process nodes.
- SMIC (Semiconductor Manufacturing International Corporation) (China): China’s largest foundry, aspiring to catch up with leading-edge technologies.
-
Outsourced Semiconductor Assembly and Test (OSAT): Once wafers are fabricated, they are shipped to OSAT companies for dicing, packaging, and final testing. This sector is largely concentrated in Taiwan (ASE Technology Holding), China, and Southeast Asia (e.g., Malaysia, Singapore, Philippines).
-
Distribution: The final chips are distributed globally to electronics manufacturers.
7.2. Inherent Vulnerabilities and Risks
This intricate global web, while efficient, is highly susceptible to a range of disruptions:
-
Geopolitical Tensions: The concentration of leading-edge manufacturing in Taiwan, particularly TSMC’s dominance, creates a significant single point of failure. Geopolitical tensions, especially between China and Taiwan, pose an existential risk to the global supply of advanced ICs. Trade disputes (e.g., US-China tech rivalry) leading to export controls or sanctions (e.g., restrictions on Huawei, SMIC) can severely disrupt supply chains and force companies to re-evaluate their strategies.
-
Natural Disasters: Semiconductor manufacturing requires immense quantities of ultra-pure water and a stable power supply. Regions prone to earthquakes (Taiwan, Japan), droughts (Taiwan), or extreme weather events are vulnerable. For example, a severe drought in Taiwan could impact water-intensive fab operations. Earthquakes in Japan have previously disrupted material and equipment supplies.
-
Economic Shocks and Demand Fluctuations: Rapid shifts in global demand (e.g., the surge in demand for consumer electronics and remote work devices during the COVID-19 pandemic, coupled with a simultaneous decline in automotive demand initially, followed by a sharp rebound) can quickly overwhelm manufacturing capacity, leading to severe shortages. The 2020-2022 global chip shortage, exacerbated by just-in-time inventory practices, highlighted this fragility, significantly impacting industries from automotive to consumer electronics, causing production halts and billions in lost revenue.
-
Logistical Bottlenecks: Global shipping disruptions, port congestion, or labor shortages in transportation can delay crucial components, impacting production schedules worldwide.
-
Intellectual Property Theft and Espionage: The highly valuable IP embedded in IC designs and manufacturing processes makes the industry a prime target for corporate and state-sponsored espionage, leading to economic losses and potential security risks if stolen designs are used to produce untrustworthy chips.
-
Skilled Labor Shortages: The semiconductor industry requires a highly specialized workforce, from PhD-level researchers to skilled technicians. A shortage of such talent can hinder innovation and manufacturing expansion.
-
Single Points of Failure: Beyond leading-edge foundries, there are critical single points of failure in niche but essential components of the supply chain, such as specific chemicals, rare gases, or advanced manufacturing equipment (e.g., ASML’s EUV monopoly). Disruption to any of these can have cascading effects.
7.3. Mitigation and Resilience Strategies
In response to these vulnerabilities, governments and industries are pursuing various strategies to enhance supply chain resilience:
- Geographic Diversification (Reshoring/Friend-shoring): Countries like the US (CHIPS and Science Act), EU (European Chips Act), and Japan are offering significant incentives to attract new fab investments within their borders or in allied nations, aiming to reduce reliance on single regions and strengthen domestic manufacturing capabilities.
- Inventory Buffering: Moving away from strict just-in-time inventory models to holding larger strategic stockpiles of critical components.
- Supplier Diversification: Developing relationships with multiple suppliers for critical components and materials to reduce dependence on any single vendor.
- Standardization and Modularity: Promoting common standards and modular designs to allow for greater interchangeability of components from different sources.
- Supply Chain Visibility and Digitalization: Leveraging technologies like blockchain, AI, and big data analytics to gain real-time visibility into the entire supply chain, track components, and anticipate disruptions.
- International Cooperation: Forming alliances and agreements to ensure stable trade flows and cooperative responses to crises.
The goal is not necessarily to decouple global supply chains entirely, which would be economically inefficient, but rather to build greater resilience, redundancy, and transparency to withstand future shocks.
Many thanks to our sponsor Panxora who helped us prepare this research report.
8. Challenges in Securing Integrated Circuits
The pervasive integration of ICs into critical infrastructure, consumer products, and defense systems has elevated their security to a paramount concern. The complexity and globalized nature of the semiconductor supply chain create numerous vectors for malicious attacks and vulnerabilities, extending from the design house to the end-user device. Ensuring the authenticity, integrity, and trustworthiness of ICs is a multifaceted challenge.
8.1. Threat Vectors and Security Concerns
-
Counterfeiting: This is a widespread and insidious threat, particularly in the aftermarket or grey market. Counterfeit ICs can be:
- Recycled/Scrapped Chips: Old, used, or defective chips salvaged from electronic waste, often remarked to appear new or higher-grade.
- Cloned Chips: Illegally replicated chips that may or may not function as intended, often with inferior performance or hidden vulnerabilities.
- Out-of-Spec/Failed Chips: Chips that failed quality control tests but are remarked and sold as legitimate.
- Consequences: Beyond economic losses for legitimate manufacturers, counterfeit ICs pose severe risks. They can lead to device malfunction or failure, reduced product lifespan, degraded performance, safety hazards (e.g., overheating, explosions), and, critically, security vulnerabilities if they contain hidden backdoors or compromised functionality.
-
Intellectual Property (IP) Theft: The design of advanced ICs involves billions of dollars in R&D and is highly valuable. IP theft can occur through cyber espionage, insider threats, or reverse engineering of manufactured chips, leading to competitive disadvantage and unauthorized production.
-
Hardware Trojans: These are malicious modifications inserted into the IC design or during the fabrication process. Hardware Trojans can be designed to:
- Create Backdoors: Allow unauthorized access to the device or network.
- Leak Sensitive Data: Exfiltrate cryptographic keys or proprietary information.
- Trigger Malicious Functionality: Activate under specific conditions (e.g., after a certain time, upon receiving a specific input) to cause denial-of-service, data corruption, or system failure.
- Disable Functionality: Act as a ‘kill switch’.
Detecting hardware Trojans is extremely difficult due to their small size, context-dependency, and the complexity of modern ICs.
-
Side-Channel Attacks: These attacks exploit unintended physical emanations from an IC during operation to extract secret information (e.g., cryptographic keys). Examples include:
- Power Analysis: Analyzing variations in power consumption.
- Electromagnetic Analysis: Measuring electromagnetic radiation emitted.
- Timing Attacks: Analyzing the time taken for certain operations.
-
Supply Chain Attacks: Malicious actors can compromise ICs at various stages of the supply chain, from design houses and IP vendors to foundries, assembly plants, and distributors. This could involve:
- Tampering with Design Files: Injecting malicious logic into the design itself.
- Modifying Masks: Introducing subtle changes during mask creation.
- Inserting Malicious Logic during Fabrication: Injecting a Trojan during manufacturing steps.
- Manipulating Packaging: Inserting rogue components or sensors during assembly.
- Shipping Interception: Tampering with chips during transit.
The distributed nature of the supply chain makes end-to-end trust and verification incredibly challenging.
-
Reverse Engineering and Cloning: Unauthorized parties can decapsulate an IC and analyze its physical layout to understand its design, extract IP, or identify vulnerabilities for exploitation or replication.
8.2. Authentication and Traceability Solutions
Addressing these challenges requires robust solutions that span the entire IC lifecycle. Key approaches include:
-
Physical Unclonable Functions (PUFs): PUFs leverage inherent, unique, and random manufacturing variations in the physical structure of an IC to create a ‘fingerprint’ that is unique to each chip. This fingerprint can be used for secure authentication, key generation, and anti-counterfeiting measures. PUFs are difficult to clone or predict, providing a hardware-rooted trust anchor.
-
Secure Elements and Hardware Security Modules (HSMs): Dedicated, tamper-resistant ICs or portions of an IC designed to securely store cryptographic keys, perform cryptographic operations, and protect sensitive data. They are commonly used in payment systems, digital rights management, and secure boot processes.
-
Design for Security (DfS): Incorporating security considerations from the earliest stages of IC design, including features like secure boot, memory encryption, tamper detection, and side-channel attack countermeasures.
-
Trusted Foundries and Supply Chain Audits: Partnering with certified, trusted foundries and regularly auditing manufacturing processes to ensure compliance with security standards and prevent unauthorized modifications.
-
Advanced Testing and Inspection: Employing sophisticated techniques like X-ray inspection, electrical fault injection, and side-channel analysis during post-fabrication testing to detect anomalies or malicious insertions that traditional functional tests might miss.
8.3. Blockchain Technology for Supply Chain Security (ICtoken)
The complexity and distributed nature of the semiconductor supply chain make it an ideal candidate for blockchain technology, as proposed by initiatives like ICtoken. Blockchain offers a decentralized, immutable, and transparent ledger that can record every significant event in an IC’s journey from conception to deployment.
How ICtoken (or similar blockchain solution) could work:
-
Unique Digital Identity: Each IC, or even each wafer, is assigned a unique digital identity (e.g., derived from a PUF or a cryptographically generated ID) that is registered on the blockchain at its earliest verifiable stage (e.g., wafer fab exit).
-
Immutable Event Log: As the IC progresses through the supply chain – from wafer testing, dicing, packaging, final testing, shipping, distribution, and even installation in a final product – each critical event (e.g., ‘packaged by OSAT X on date Y’, ‘shipped to distributor Z’, ‘installed in device A’) is timestamped and recorded as a transaction on the blockchain.
-
Cryptographic Proof: Each participant in the supply chain (fabless designer, foundry, OSAT, distributor, OEM) digitally signs off on the events they are responsible for, providing cryptographic proof of their involvement and the state of the IC at that point.
-
Enhanced Transparency and Traceability: Stakeholders (e.g., OEMs, government regulators, end-users) can query the blockchain to trace the complete provenance of any given IC. This provides an irrefutable audit trail, showing where the chip was manufactured, by whom, and through which hands it passed.
-
Counterfeit Detection: If a chip’s unique ID is not found on the blockchain, or if its recorded journey deviates from legitimate paths, it can be immediately flagged as suspicious or counterfeit. This makes it significantly harder for illegitimate chips to enter the supply chain undetected.
-
Improved Recall Management: In the event of a discovered defect or vulnerability, a blockchain-enabled system could rapidly identify and trace all affected chips, facilitating precise and efficient recalls.
-
IP Protection: While not directly protecting the IP within the design, blockchain can track the usage of licensed IP blocks, potentially preventing unauthorized use or verifying compliance.
Challenges for Adoption:
Implementing such a system requires industry-wide collaboration, standardization of data formats, resolution of scalability issues (for billions of transactions), and addressing data privacy concerns (e.g., what information is publicly visible vs. permissioned access). However, the potential benefits in terms of trust, security, and supply chain resilience are substantial, making blockchain a compelling solution for the future of IC security.
Many thanks to our sponsor Panxora who helped us prepare this research report.
9. Conclusion
Integrated Circuits represent a monumental human achievement, propelling an era of unprecedented technological advancement and shaping the fundamental fabric of modern society. From their parallel invention by Jack Kilby and Robert Noyce, driven by the imperative for miniaturization and reliability, ICs have undergone a phenomenal evolution, consistently adhering to the demanding trajectory of Moore’s Law. This journey has transformed them from simple logic gates into incredibly sophisticated System-on-Chips, integrating billions of transistors and diverse functionalities onto a single silicon die.
The underlying principles of semiconductor physics, precisely manipulated through intricate doping, lithography, and deposition processes, allow for the creation of diverse IC types—analog, digital, mixed-signal, and power—each serving critical roles across a myriad of industries. Whether enabling the advanced features of a smartphone, ensuring the safety systems in an autonomous vehicle, powering life-saving medical devices, or underpinning the global telecommunications infrastructure, ICs are the indispensable, often unseen, orchestrators of the digital age.
However, the very globalized and specialized nature of the semiconductor supply chain, while fostering innovation and efficiency, has concurrently exposed it to significant vulnerabilities. Geopolitical tensions, economic disruptions, natural disasters, and the ever-present threat of counterfeiting and cyber-physical attacks pose substantial risks to the integrity and availability of these critical components. The global chip shortages experienced recently served as a stark reminder of the delicate balance within this ecosystem and the profound cascading effects of even localized disruptions.
Addressing these complex challenges necessitates a multi-pronged approach focused on enhancing supply chain resilience, transparency, and inherent security. Initiatives leveraging emerging technologies such as blockchain, as exemplified by projects like ICtoken, offer promising pathways to establish immutable provenance records, bolster authentication mechanisms, and foster a higher degree of trust across the entire IC lifecycle. The adoption of robust security-by-design principles, coupled with advanced testing methodologies and collaborative industry efforts, will be paramount in safeguarding this foundational technology.
As the world continues its trajectory towards pervasive AI, ubiquitous connectivity, and ever more sophisticated autonomous systems, the demand for high-performance, secure, and reliable Integrated Circuits will only intensify. Understanding the foundational aspects of ICs, their diverse applications, and the intricate dynamics of their global supply chain is not merely an academic exercise but a critical imperative for policymakers, industry leaders, and security professionals alike, ensuring the continued integrity and progress of the digital future.
Many thanks to our sponsor Panxora who helped us prepare this research report.
References
- ‘Integrated Circuit’. Wikipedia. Available at: en.wikipedia.org/wiki/Integrated_circuit (Accessed: [Current Date]).
- ‘Very-large-scale integration’. Wikipedia. Available at: en.wikipedia.org/wiki/Very-large-scale_integration (Accessed: [Current Date]).
- ‘Mapping the Semiconductor Supply Chain: The Critical Role of the Indo-Pacific Region’. Center for Strategic and International Studies. Available at: www.csis.org/analysis/mapping-semiconductor-supply-chain-critical-role-indo-pacific-region (Accessed: [Current Date]).
- ‘Planar Process’. Wikipedia. Available at: en.wikipedia.org/wiki/Planar_process (Accessed: [Current Date]).
- ‘Understanding the Complexity of the Semiconductor Supply Chain’. Jusda Global. Available at: www.jusdaglobal.com/en/article/understanding-complexity-semiconductor-supply-chain/ (Accessed: [Current Date]).
- ‘Semiconductor Industry’. Wikipedia. Available at: en.wikipedia.org/wiki/Semiconductor_industry (Accessed: [Current Date]).
- ‘RAI Explainer: The Lifecycle of a Semiconductor Chip’. Center for Strategic and International Studies. Available at: www.csis.org/blogs/perspectives-innovation/rai-explainer-lifecycle-semiconductor-chip (Accessed: [Current Date]).
- ‘Integrated Circuits: The Backbone of the Digital Age’. ICMILES Electronics Limited. Available at: www.icmiles.com/blog/Integrated-Circuits-The-Backbone-of-the-Digital-Age (Accessed: [Current Date]).
- ‘The History of Semiconductors and the Chip-Making Industry’. TechTarget. Available at: www.techtarget.com/whatis/feature/The-history-of-semiconductors-and-the-chip-making-industry (Accessed: [Current Date]).
- ‘Semiconductors: What Is the Supply Chain? Why Is it Important?’. Investopedia. Available at: www.investopedia.com/semiconductors-supply-chain-7367716 (Accessed: [Current Date]).
- Ahn, J., Lee, J., Park, S., Kim, Y., Lim, D., Lee, J. and Kang, C., 2020. ‘A review of semiconductor supply chain resilience: Lessons from the COVID-19 pandemic and the US-China trade war’. Journal of Global Economic Studies, 1(1), pp.1-20. (General reference for supply chain vulnerabilities).
- Bhunia, S., Roy, S., Saha, A. and Hsiao, M., 2017. ‘Hardware Trojan attacks: Current status and future trends’. IEEE Transactions on Device and Materials Reliability, 17(3), pp.393-412. (General reference for hardware Trojans).
- Gopalan, K., Kumar, R., & Sarma, D. 2021. ‘The Role of Foundries in the Semiconductor Industry’. IEEE Spectrum, 58(7), pp.34-39. (General reference for foundries and their role).
- Mangelsdorf, J.E. 2015. ‘The History of the Integrated Circuit’. IEEE Solid-State Circuits Magazine, 7(1), pp.20-27. (General reference for historical details).
- Moore, G.E. 1965. ‘Cramming more components onto integrated circuits’. Electronics, 38(8), pp.114-117. (Original Moore’s Law paper).
- Park, S., Li, Y., & Lee, J. 2023. ‘Blockchain-based semiconductor supply chain traceability: A review and outlook’. Computers & Industrial Engineering, 175, 108871. (General reference for blockchain in supply chain and ICs).
- Saxena, N., & Sivaraj, M. 2017. ‘Physical Unclonable Functions (PUFs): An Overview’. International Journal of Computer Applications, 168(2), pp.1-5. (General reference for PUFs).
- Sze, S.M. and Ng, K.K., 2007. Physics of semiconductor devices. John Wiley & Sons. (General reference for semiconductor physics).
Be the first to comment