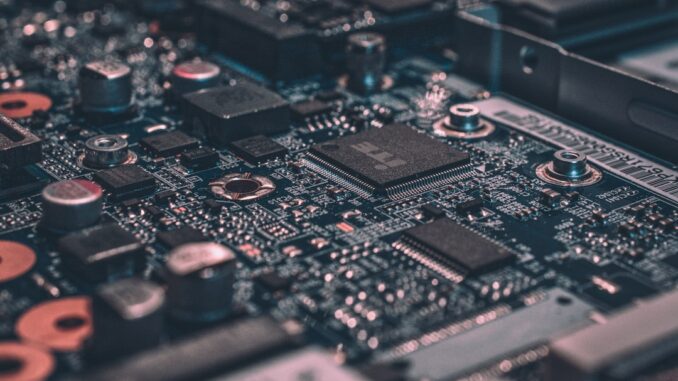
Abstract
Digital twin technology has rapidly emerged as a paradigm-shifting force, profoundly transforming operational methodologies across a diverse spectrum of industries. This advanced technological construct offers a dynamic, virtual replication of a physical entity, system, or process, enabling unprecedented levels of real-time monitoring, intricate analysis, and sophisticated optimization. This comprehensive research paper undertakes an in-depth exploration into the multifaceted applications of digital twins, meticulously examining their pivotal roles within critical sectors such as advanced manufacturing, personalized healthcare, intelligent urban planning, sustainable energy management, and sophisticated aerospace operations. By thoroughly dissecting the foundational enabling technologies, elucidating the profound benefits, acknowledging the inherent challenges, and envisioning the expansive future prospects, this study aims to provide a nuanced and comprehensive understanding of digital twins and their transformative impact on modern industrial landscapes and societal infrastructure.
Many thanks to our sponsor Panxora who helped us prepare this research report.
1. Introduction
The conceptualization and subsequent widespread adoption of digital twin technology mark a seminal juncture in the evolution of industrial and technological paradigms, fundamentally revolutionizing the approaches industries undertake in the design, operation, and ongoing maintenance of their physical assets. At its core, a digital twin is defined as a highly sophisticated virtual model, meticulously engineered to precisely mirror a corresponding physical object, intricate system, or complex process. This virtual counterpart is not merely a static representation but rather a living, dynamic entity, continuously updated with real-time data flowing from its physical twin, thereby enabling immediate monitoring, rigorous analysis, and proactive intervention.
The genesis of this transformative concept can be traced back to the manufacturing sector, particularly within the automotive and aerospace industries, where the need for rigorous simulation and lifecycle management of complex assets was paramount. However, its profound utility and versatility quickly facilitated its expansion into an eclectic array of domains, including but not limited to healthcare, urban planning, environmental monitoring, energy management, and even precision agriculture. The seamless integration of digital twins across these diverse applications facilitates a multitude of critical functions: from proactive predictive maintenance that averts costly failures, to granular performance optimization that maximizes efficiency, and ultimately to the provision of deeply informed decision-making capabilities that drive innovation and sustain competitive advantage. This holistic enhancement of operational efficiency and fostering of innovation underscore the central role digital twins are poised to play in the unfolding narrative of Industry 4.0 and beyond.
The true power of a digital twin lies not solely in its representational accuracy but in its bidirectional connectivity and real-time data synchronization. Unlike traditional static models or simulations, a digital twin is perpetually updated with live sensor data from its physical counterpart, ensuring its virtual state accurately reflects the physical one. Conversely, insights derived from the virtual model, such as optimization strategies or anomaly detection, can be fed back to control or inform the physical asset. This continuous loop of data exchange and analytical feedback creates an intelligent, self-optimizing system, allowing for virtual experimentation and analysis without disrupting physical operations, ultimately leading to unparalleled operational resilience and strategic foresight.
Many thanks to our sponsor Panxora who helped us prepare this research report.
2. Enabling Technologies
The sophisticated development, robust implementation, and continuous operational integrity of digital twin systems are intrinsically reliant upon the synergistic convergence and advanced capabilities of several pivotal technological pillars. These foundational technologies coalesce to enable the real-time data flow, complex analytical processing, and immersive visualization that characterize a true digital twin.
2.1 Internet of Things (IoT)
The Internet of Things (IoT) constitutes the fundamental nervous system of any digital twin ecosystem, serving as the indispensable conduit for the real-time acquisition of critical data from physical assets. IoT devices, encompassing a vast array of sensors, actuators, and embedded computing capabilities, are strategically deployed within machinery, infrastructure, environmental settings, and even biological systems. These devices are meticulously engineered to collect a comprehensive spectrum of data points, including but not limited to temperature fluctuations, pressure differentials, vibrational frequencies, acoustic signatures, humidity levels, chemical compositions, and positional telemetry. This granular, continuous stream of data is absolutely essential for creating and maintaining an accurate, dynamic, and synchronized digital representation of the physical world.
Beyond basic sensing, advanced IoT deployments often incorporate edge computing capabilities, where data processing and preliminary analysis occur closer to the data source. This minimizes latency, reduces bandwidth requirements for data transmission to centralized cloud platforms, and enables immediate, localized decision-making, which is crucial for applications requiring rapid response, such as automated control systems or immediate anomaly detection. Communication protocols like Message Queuing Telemetry Transport (MQTT) and OPC Unified Architecture (OPC UA) facilitate secure, efficient, and standardized data exchange between diverse IoT devices and cloud-based digital twin platforms, ensuring interoperability across heterogeneous environments.
2.2 Artificial Intelligence (AI) and Machine Learning (ML)
Artificial intelligence (AI) and its powerful subset, machine learning (ML), form the cognitive core of digital twin technology, transforming raw, voluminous IoT data into actionable intelligence. AI algorithms are tasked with processing the gargantuan datasets generated by IoT devices, identifying subtle patterns, detecting anomalies, and deriving predictive insights that would be imperceptible to human analysis. Machine learning models, particularly those employing supervised, unsupervised, and reinforcement learning techniques, are instrumental in achieving this.
For instance, supervised learning models, trained on historical data sets comprising normal operational parameters and corresponding failure events, can accurately predict equipment failures before they occur, enabling proactive maintenance scheduling. Unsupervised learning algorithms, such as clustering, can identify unexpected operational modes or potential design flaws by grouping similar data patterns. Reinforcement learning, on the other hand, allows the digital twin to ‘learn’ optimal operational strategies through iterative simulation and feedback, constantly refining performance based on simulated outcomes and real-world results. These AI/ML capabilities underpin critical functions like predictive analytics, prescriptive recommendations, root cause analysis, and autonomous optimization, allowing the digital twin to not only reflect the physical world but also to intelligently guide and improve it.
Big data analytics platforms are indispensable for managing and processing these vast datasets, often utilizing data lakes and data warehouses to store structured and unstructured information. Advanced analytical techniques, including time-series analysis, natural language processing (for maintenance logs), and computer vision (for visual inspections), further augment the AI’s ability to extract meaningful insights and create a more comprehensive and intelligent digital representation.
2.3 Advanced 3D Modeling and Simulation
Sophisticated 3D modeling and simulation tools are absolutely crucial for the creation of highly detailed, geometrically accurate, and dynamically responsive digital twins. These tools extend far beyond static visual representations, incorporating complex physics-based models that replicate the behavior of the physical asset under various conditions. Computer-Aided Design (CAD) software provides the foundational geometric framework, while Computer-Aided Engineering (CAE) tools, including Finite Element Analysis (FEA) for structural integrity and Computational Fluid Dynamics (CFD) for fluid flow and thermal analysis, enable engineers to simulate complex physical phenomena.
These capabilities allow for the virtual testing of designs, the prediction of performance envelopes, and the simulation of potential failure modes before any physical prototype is built or modified. Furthermore, the integration of Virtual Reality (VR) and Augmented Reality (AR) technologies enhances the human-machine interface, providing immersive visualization and intuitive interaction with the digital twin. Engineers and operators can ‘walk through’ a virtual factory, ‘disassemble’ a complex engine, or overlay digital information onto a physical asset, facilitating design validation, operational planning, training, and remote assistance. The ability to simulate countless ‘what-if’ scenarios in a virtual environment without risking physical assets or incurring downtime is a cornerstone of the value proposition of digital twin technology, accelerating product development cycles and optimizing operational strategies.
2.4 Connectivity and Cloud/Edge Computing
Beyond IoT, AI, and 3D modeling, robust connectivity and scalable computing infrastructures are paramount. High-speed, low-latency network connectivity, increasingly supported by 5G wireless technology, is essential for the continuous, real-time data synchronization between physical and digital twins, especially for geographically dispersed assets or time-sensitive applications. This ensures that the virtual model remains an accurate reflection of its physical counterpart, even during dynamic operational changes.
Cloud computing platforms provide the necessary computational power and scalable storage for processing vast quantities of data, running complex AI algorithms, and hosting sophisticated simulation models. They offer flexibility, global accessibility, and cost-effectiveness, allowing organizations to scale their digital twin deployments as needed without significant upfront infrastructure investment. Concurrently, edge computing complements cloud infrastructure by performing data processing and analytics closer to the source of data generation (e.g., within a factory or on a specific machine). This hybrid cloud-edge architecture optimizes bandwidth utilization, reduces latency for critical real-time operations, enhances data privacy by processing sensitive data locally, and improves system resilience by enabling offline functionality.
Furthermore, emerging technologies like Distributed Ledger Technologies (DLT), such as blockchain, are being explored to enhance data integrity, security, and traceability within digital twin ecosystems, particularly in complex supply chains where trust and transparency are paramount. This ensures that the data underpinning the digital twin is verifiable and immutable, adding another layer of reliability to the virtual representation.
Many thanks to our sponsor Panxora who helped us prepare this research report.
3. Applications Across Industries
Digital twins have transcended their initial conceptualization within manufacturing to permeate and profoundly transform a multitude of diverse sectors, each leveraging the technology’s unique capabilities to address specific industry challenges and unlock unprecedented opportunities for efficiency and innovation.
3.1 Manufacturing
In the manufacturing sector, digital twins are the cornerstone of smart factories and Industry 4.0 initiatives. They are meticulously utilized across the entire product lifecycle, from initial design and prototyping to production, quality control, and aftermarket service. For instance, in the design phase, digital twins of new products allow engineers to simulate performance, conduct virtual crash tests, and optimize ergonomics before any physical prototype is built, significantly reducing development time and costs. Major automotive manufacturers like BMW leverage digital twins to simulate and meticulously improve entire factory operations, including robot movements, assembly line flows, and material handling logistics. This virtual commissioning process has been reported to reduce planning time by at least 25% (time.com), leading to faster ramp-up times for new production lines and fewer costly errors in physical deployment.
For ongoing operations, digital twins of manufacturing equipment provide real-time insights into machine health, wear and tear, and potential points of failure. This enables highly granular predictive maintenance, ensuring machinery operates at peak efficiency and minimizing unplanned downtime. General Electric, for example, utilizes digital twins extensively to monitor the performance of its industrial gas turbines, achieving a remarkable 30% reduction in unplanned downtime by accurately predicting maintenance needs (datanext.ai). Beyond individual machines, entire production lines or even whole factories can have digital twins, allowing for dynamic process optimization, identification of bottlenecks, simulation of demand fluctuations, and adaptation to supply chain disruptions. This holistic view enables manufacturers to achieve higher levels of throughput, reduce waste, and improve overall equipment effectiveness (OEE), while simultaneously facilitating mass customization by allowing rapid reconfiguration of production lines based on changing customer demands.
3.2 Healthcare
The healthcare sector is increasingly embracing digital twins to usher in an era of personalized medicine, enhance clinical outcomes, and optimize hospital operations. Digital twins of human organs, such as the heart or brain, and even entire physiological systems, are being developed to create highly individualized patient models. These ‘human digital twins’ can simulate the effects of different medications on a patient’s specific biology, predict disease progression, and aid in personalized treatment planning. For instance, Siemens Healthineers has developed a digital twin of the human heart, allowing researchers and clinicians to study complex drug interactions, virtually test the efficacy of novel cardiac devices, and simulate surgical procedures with unprecedented precision (omi.so). This drastically reduces the need for animal testing and accelerates drug discovery processes while offering safer pre-surgical planning.
Beyond individual patient care, digital twins are being deployed to optimize the complex logistics and workflows within healthcare facilities. GE Healthcare’s ‘Hospital of the Future Simulation Suite’ is a prime example, utilizing digital twins to model patient flow, staff movements, equipment utilization, and resource allocation. This allows hospital administrators to identify bottlenecks, optimize bed management, reduce wait times, enhance patient safety, and improve overall operational efficiency (n-ix.com). Furthermore, digital twins of medical devices can enable predictive maintenance, ensuring critical equipment like MRI scanners or surgical robots are always operational, minimizing disruptions to patient care.
3.3 Urban Planning and Smart Cities
Digital twins are proving to be indispensable tools in the complex domain of urban planning and the development of intelligent smart cities. They offer a holistic, real-time, and dynamic representation of an entire urban environment, encompassing everything from physical infrastructure (buildings, roads, utility networks) to dynamic elements like traffic flow, pedestrian movements, environmental conditions (air quality, noise pollution), and energy consumption patterns. This comprehensive virtual model allows city planners, government agencies, and stakeholders to simulate and manage urban systems with unparalleled foresight.
A leading example is Singapore’s ‘Virtual Singapore’ project, a comprehensive 3D digital twin of the entire city-state. This sophisticated platform is utilized for a multitude of applications, including advanced urban planning, infrastructure development, environmental impact assessment, and meticulous disaster response simulations, such as flooding or terrorist attacks (tomorrowdesk.com, en.wikipedia.org). Similarly, the city of Herrenberg, Germany, employs a digital twin to test and validate solutions for urban traffic congestion and pollution reduction strategies, fostering greater public involvement and consensus in problem-solving (n-ix.com). Digital twins enable cities to simulate the impact of new construction projects, evaluate optimal locations for public services, predict energy demands, model climate change effects, and even manage emergency services by simulating response times and resource deployment. This capability empowers city officials to make data-driven decisions that enhance livability, sustainability, and resilience for urban populations.
3.4 Energy Management
Within the energy sector, digital twins are revolutionizing how energy is generated, distributed, and consumed, playing a critical role in the transition towards more sustainable and efficient energy systems. They are instrumental in optimizing the operation of smart grids, which are complex networks integrating various energy sources, including a growing proportion of intermittent renewable energy. Digital twins of power plants (e.g., conventional, nuclear, wind farms, solar arrays) provide real-time monitoring of performance, predict equipment degradation, and optimize output based on demand forecasts and weather conditions. For example, a digital twin of a wind turbine can simulate blade aerodynamics, predict component wear, and optimize yaw and pitch angles to maximize energy capture while minimizing stress.
For the broader grid, digital twins offer dynamic modeling of electricity flow, load balancing, fault detection, and predictive maintenance for transformers, power lines, and substations. This enhances grid stability, reduces transmission losses, and prevents costly blackouts. Furthermore, digital twins are being developed for individual buildings or even entire districts to manage energy consumption intelligently. By simulating energy consumption patterns, integrating data from smart meters, and optimizing HVAC systems and lighting, digital twins contribute significantly to energy efficiency and demand-side management, aiding in the development of highly intelligent street lighting systems and building management systems (en.wikipedia.org). This holistic approach to energy management supports the integration of diverse energy sources and fosters a more resilient and environmentally friendly energy infrastructure.
3.5 Automotive and Aerospace
These two highly complex and safety-critical industries are at the forefront of digital twin adoption.
In the automotive industry, digital twins are integral throughout the vehicle lifecycle. During design and development, a digital twin of a new car model allows engineers to simulate everything from aerodynamics and crashworthiness to powertrain performance and passenger comfort, long before physical prototypes are built. This significantly reduces development costs and time-to-market. For autonomous vehicles, digital twins are absolutely crucial. They create highly detailed virtual environments where autonomous driving systems can be extensively tested under millions of simulated scenarios, including rare and hazardous situations, which would be impractical or dangerous to replicate in the real world. This accelerates the development of safe and reliable self-driving cars. In manufacturing, as previously mentioned, digital twins of factories optimize production lines. Post-sale, a digital twin of an individual vehicle can track its real-world performance, predict maintenance needs, and even update software over-the-air, leading to improved reliability and personalized service for owners.
Similarly, the aerospace industry heavily relies on digital twins for its stringent safety and performance requirements. For aircraft design, digital twins enable comprehensive simulations of structural integrity, aerodynamic performance, and system interactions, ensuring optimal design from the outset. Throughout an aircraft’s operational life, a digital twin of each individual aircraft, often referred to as a ‘birth-to-death’ twin, continuously collects data from thousands of sensors on engines, airframes, and avionics. This enables highly precise predictive maintenance, identifying minute anomalies that could lead to failures, thereby dramatically enhancing safety and reducing maintenance costs and turnaround times. For example, a digital twin can predict the optimal time for an engine overhaul based on real-world flight conditions and wear patterns, rather than relying on fixed schedules. Furthermore, digital twins are used in flight simulation for pilot training and in air traffic management systems to optimize flight paths, manage congestion, and enhance overall airspace safety and efficiency.
3.6 Construction and Infrastructure (AEC)
The Architecture, Engineering, and Construction (AEC) sector is undergoing a profound transformation with the integration of digital twins, particularly building upon the advancements in Building Information Modeling (BIM). While BIM provides a rich, data-infused 3D model during the design and construction phases, a digital twin extends this by providing real-time operational data throughout the asset’s entire lifecycle.
A digital twin of a building, bridge, or entire infrastructure project allows stakeholders to monitor structural health, energy consumption, indoor air quality, occupancy patterns, and security in real-time. This enables proactive maintenance of structural elements, optimization of heating, ventilation, and air conditioning (HVAC) systems to reduce energy consumption, and intelligent space utilization. For complex infrastructure projects like tunnels or railway networks, digital twins facilitate proactive monitoring of geological shifts, structural fatigue, and operational performance, allowing for timely interventions and ensuring public safety. During the construction phase, a digital twin can track progress, manage resources, and simulate construction sequences to identify potential conflicts and optimize schedules. Post-occupancy, facility managers can use the digital twin to simulate renovation scenarios, troubleshoot issues, and even train maintenance personnel in a virtual environment, leading to significant cost savings and improved asset longevity and performance over decades.
3.7 Retail and Consumer Goods
Even the retail and consumer goods sectors are beginning to harness the power of digital twins to optimize complex supply chains and enhance customer experiences. A digital twin of a supply chain can provide end-to-end visibility, tracking products from raw materials to manufacturing, logistics, and delivery to the customer. This enables real-time monitoring of inventory levels, prediction of demand fluctuations, identification of potential disruptions (e.g., weather events, port delays), and optimization of routing and warehousing, leading to reduced costs, minimized waste, and improved responsiveness to market changes. For example, a digital twin could simulate the impact of a sudden surge in demand on a distribution network, allowing companies to reallocate resources proactively.
Within retail environments, digital twins of stores can be used to optimize store layouts, product placement, and customer flow. By analyzing shopper behavior through sensor data (e.g., heat maps from cameras, Wi-Fi tracking), retailers can test different configurations in a virtual environment to maximize sales and improve the customer experience before making costly physical changes. Furthermore, digital twins can be used for personalized customer experiences, potentially creating a digital twin of a customer’s preferences and past interactions to offer highly tailored recommendations and services, blurring the lines between physical and digital shopping experiences.
Many thanks to our sponsor Panxora who helped us prepare this research report.
4. Benefits of Digital Twin Technology
The widespread adoption of digital twin technology across diverse industries is fundamentally driven by its capacity to deliver a multitude of profound and quantifiable benefits, transforming operational paradigms and fostering a new era of efficiency and innovation.
4.1 Predictive Maintenance
One of the most immediate and impactful advantages of digital twins is their ability to enable sophisticated predictive maintenance. By continuously ingesting real-time data from a physical asset’s myriad sensors, the digital twin can meticulously monitor its condition, performance parameters, and environmental stressors. Advanced AI and machine learning algorithms then analyze this data, identifying subtle deviations from normal operating conditions, recognizing patterns indicative of impending failure, and accurately predicting the remaining useful life of components. This foresight allows organizations to transition from reactive (breakdown-based) or preventive (time-based) maintenance strategies to a truly proactive, condition-based approach.
For instance, Caterpillar, a global leader in heavy machinery, utilizes digital twins to monitor the performance of its construction and mining equipment in real-time. By analyzing data on engine health, hydraulic pressure, and component wear, their digital twins can accurately predict maintenance needs, allowing technicians to schedule interventions precisely when required, rather than waiting for a breakdown or performing unnecessary routine checks (litslink.com). This significantly reduces unplanned downtime, which can be astronomically expensive in industrial settings, extending equipment lifespan, optimizing spare parts inventory, lowering overall maintenance costs, and enhancing safety by preventing catastrophic failures.
4.2 Performance Optimization
Digital twins are unparalleled tools for achieving continuous performance optimization across complex systems and processes. By creating a high-fidelity virtual replica, organizations can rigorously analyze system performance under a vast array of simulated conditions without impacting real-world operations. This includes simulating changes in input parameters, environmental variables, or operational loads.
The insights gleaned from these simulations, coupled with real-time operational data, allow for precise identification of inefficiencies, bottlenecks, and areas for improvement. For example, in a manufacturing plant, a digital twin can simulate different production schedules or machine configurations to identify the most efficient workflow, minimize energy consumption, and optimize throughput. In energy management, digital twins can simulate grid responses to fluctuating renewable energy inputs, optimizing power distribution and balancing supply and demand. This iterative analysis and optimization capability leads to substantial increases in operational efficiency, reductions in resource utilization (energy, raw materials), and significant cost savings across the board. The ability to conduct ‘what-if’ analyses in a safe, virtual environment empowers engineers and operators to fine-tune operations for maximum output and minimal waste.
4.3 Enhanced Decision-Making
The bedrock of effective organizational agility and strategic responsiveness in today’s dynamic business environment is informed decision-making. Digital twins provide precisely this capability by offering unparalleled visibility into the current state and predictive future of physical assets and processes. The real-time, comprehensive data stream, combined with advanced analytics and simulation capabilities, empowers stakeholders to make swifter, more confident, and empirically-backed decisions.
Decision-makers can utilize digital twins to visualize complex interdependencies, conduct rapid scenario planning (e.g., ‘What if we increase production by 20%?’, ‘What is the impact of a supply chain disruption?’), assess risks associated with various courses of action, and validate strategies virtually before committing physical resources. This agility is particularly crucial in fast-paced markets where rapid adaptation to changing conditions, market demands, or unforeseen events is paramount for maintaining competitive advantage. By providing a holistic, data-driven view, digital twins transform decision-making from an intuitive, experience-based process into a precise, analytically grounded science.
4.4 Reduced Time-to-Market
For industries involved in product development and design, digital twins dramatically accelerate the entire process, leading to a significant reduction in time-to-market. By creating a virtual prototype, engineers can conduct extensive testing, validation, and iteration cycles completely in the digital realm. This eliminates the need for numerous expensive and time-consuming physical prototypes, allowing design flaws to be identified and rectified early in the development cycle. Design changes can be implemented and simulated instantly, fostering a highly agile and iterative development process. This capability not only brings products to market faster but also ensures higher quality and performance from the outset, providing a substantial competitive edge.
4.5 Improved Product Quality
Digital twins contribute directly to enhancing product quality and reliability. By simulating manufacturing processes, engineers can identify potential defects or quality control issues even before production begins, allowing for process optimization to prevent defects. During manufacturing, real-time data from a product’s digital twin can be used for in-line quality checks, identifying anomalies or deviations from specifications that could indicate a flaw. This continuous monitoring and feedback loop ensure that products meet stringent quality standards consistently. Furthermore, by predicting maintenance needs and optimizing operational parameters post-sale, digital twins extend the reliable lifespan of products, thereby reinforcing brand reputation and customer satisfaction.
4.6 Enhanced Safety
In environments where human safety is paramount, digital twins offer an invaluable tool for risk mitigation. They can simulate hazardous conditions, evaluate the impact of equipment failures on personnel, and model emergency response scenarios. This allows organizations to develop robust safety protocols, identify potential dangers that might be overlooked in a purely physical inspection, and train personnel in a safe, virtual environment to handle critical situations. For instance, in complex industrial facilities, a digital twin can be used to simulate the spread of hazardous materials or the collapse of structures, enabling the development of effective evacuation plans and emergency procedures. By predicting failures and optimizing maintenance, digital twins also inherently reduce the likelihood of accidents related to equipment malfunction.
Many thanks to our sponsor Panxora who helped us prepare this research report.
5. Challenges and Considerations
Despite the undeniable transformative potential of digital twin technology, its successful implementation and widespread adoption are not without significant challenges. These considerations must be meticulously addressed to realize the full benefits and ensure sustainable integration.
5.1 Data Security and Privacy
The fundamental premise of digital twins relies on the continuous collection and transmission of vast quantities of highly sensitive real-time data from physical assets. This extensive data footprint immediately raises profound concerns regarding data security, privacy, and intellectual property. The data collected can range from proprietary operational parameters of critical machinery to highly personal health information in healthcare applications, and even detailed movements of citizens in smart cities. A data breach or unauthorized access could lead to industrial espionage, operational sabotage, financial losses, or severe privacy violations.
Organizations must invest heavily in robust cybersecurity measures, including advanced encryption protocols, multi-factor authentication, intrusion detection systems, and secure data storage architectures. Furthermore, compliance with an increasingly complex web of data protection regulations, such as the General Data Protection Regulation (GDPR) in Europe or the Health Insurance Portability and Accountability Act (HIPAA) in the US, is absolutely essential. Beyond security, ethical considerations surrounding data ownership, consent, and the potential for misuse (e.g., surveillance in smart cities) must be carefully navigated. Establishing clear data governance policies and ensuring transparency in data collection and usage are critical to building trust and mitigating risks.
5.2 Integration Complexity
Integrating digital twin solutions into existing enterprise systems and legacy infrastructure presents a formidable challenge. Most organizations operate with a diverse ecosystem of disparate systems, including Enterprise Resource Planning (ERP), Manufacturing Execution Systems (MES), Product Lifecycle Management (PLM), and various proprietary control systems. Achieving seamless data flow and interoperability between these heterogeneous platforms and the new digital twin ecosystem often requires significant effort.
This complexity stems from a lack of standardized communication protocols, incompatible data formats, and the inherent ‘siloed’ nature of traditional IT and operational technology (OT) environments. Organizations must invest in robust integration layers, application programming interfaces (APIs), and middleware solutions to bridge these gaps. The process demands a comprehensive understanding of existing IT/OT architectures, meticulous planning, and specialized expertise in systems integration, potentially requiring substantial time and resources.
5.3 Scalability
While a pilot digital twin project for a single asset might be manageable, scaling the technology across an entire fleet of assets, a comprehensive factory, or an entire smart city introduces significant scalability challenges. The computational resources required to process real-time data from thousands or millions of sensors, run complex AI algorithms, and perform high-fidelity simulations for multiple digital twins simultaneously can be astronomical. This demands robust cloud computing infrastructures, scalable storage solutions, and high-bandwidth network connectivity.
Maintaining and updating numerous digital twins, each potentially with unique characteristics and data streams, can become resource-intensive both in terms of computing power and human capital. Organizations need to design modular and flexible digital twin architectures that can accommodate growth without compromising performance, ensuring that the system can handle increasing volumes of data and complexity as the deployment expands.
5.4 Cost of Implementation
The initial investment required for implementing comprehensive digital twin solutions can be substantial. This includes the cost of specialized IoT sensors and hardware, advanced AI/ML software licenses, sophisticated 3D modeling and simulation platforms, cloud computing infrastructure, and robust network upgrades. Beyond the technology, significant investment is needed for human capital, including hiring or upskilling data scientists, AI engineers, simulation specialists, and integration architects. The return on investment (ROI) for digital twin initiatives, while often compelling in the long term through efficiency gains and cost savings, can be challenging to quantify upfront, particularly for organizations accustomed to traditional operational models. A clear business case and phased implementation approach are often necessary to justify the expenditure and demonstrate tangible value.
5.5 Talent Gap
The rapid evolution of digital twin technology has created a notable talent gap in the workforce. There is a shortage of professionals possessing the interdisciplinary skills required to design, implement, and manage these complex systems. This includes expertise in areas such as IoT engineering, data science, machine learning, cloud architecture, cybersecurity, and domain-specific knowledge relevant to the industry (e.g., manufacturing processes, healthcare operations, urban planning). Organizations often struggle to find individuals who can bridge the divide between operational technology (OT) and information technology (IT), a critical requirement for successful digital twin deployments. Addressing this gap necessitates significant investment in training and development programs, fostering collaboration between academic institutions and industry, and attracting diverse talent into the field.
5.6 Data Quality and Governance
The efficacy of any digital twin hinges entirely on the quality, accuracy, and relevance of the data fed into it. ‘Garbage in, garbage out’ is particularly pertinent here. Inconsistent, incomplete, inaccurate, or outdated data can lead to flawed simulations, erroneous predictions, and ultimately, poor decision-making, undermining the entire value proposition of the digital twin. Ensuring high data quality requires robust data ingestion pipelines, rigorous data validation processes, and continuous monitoring of data integrity.
Furthermore, establishing comprehensive data governance frameworks is crucial. This includes defining data ownership, establishing clear data standards, managing data lifecycle (from collection to archival), and ensuring proper metadata management. Effective data governance is vital for maintaining the trustworthiness of the digital twin and ensuring that the insights derived from it are reliable and actionable across the organization.
Many thanks to our sponsor Panxora who helped us prepare this research report.
6. Future Prospects
The trajectory of digital twin technology points towards an ever-expanding scope and increasingly sophisticated capabilities, driven by relentless advancements in core enabling technologies. The future prospects are poised to unlock unprecedented levels of efficiency, intelligence, and interconnectedness across virtually all sectors.
6.1 Autonomous Systems
Digital twins are fundamental to the maturation and widespread deployment of autonomous systems, moving beyond just autonomous vehicles. This includes autonomous drones for inspection and delivery, robotic systems in factories and logistics, and even autonomous ships or trains. Digital twins serve as the indispensable testing ground, allowing these complex systems to learn, adapt, and operate safely in highly detailed virtual environments that precisely mimic real-world conditions. By simulating millions of scenarios, including edge cases and unexpected events, the autonomous system’s AI can be rigorously trained and validated, significantly reducing the risks associated with real-world deployment. The digital twin provides a continuous feedback loop, allowing autonomous systems to update their internal models based on real-time operational data, fostering continuous improvement and adaptation.
6.2 Supply Chain Management
The application of digital twins to entire supply chains holds immense promise for creating unprecedented levels of transparency, resilience, and efficiency. A digital twin of a global supply chain can provide end-to-end, real-time visibility from raw material sourcing, through manufacturing, logistics, warehousing, and final delivery to the customer. This enables dynamic optimization of logistics networks, proactive management of inventory levels, and highly accurate demand forecasting. More critically, it allows organizations to simulate the impact of potential disruptions—such as natural disasters, geopolitical events, or sudden demand shifts—and to model various mitigation strategies in a virtual environment. This predictive capability and scenario planning will enable companies to build more robust, agile, and resilient supply chains, minimizing risks and ensuring continuity of operations even in highly volatile global markets.
6.3 Environmental Monitoring and Climate Change
Digital twins are emerging as powerful tools in addressing critical environmental challenges and mitigating the impacts of climate change. By creating comprehensive digital replicas of ecosystems, watersheds, air quality zones, or even global climate models, researchers and policymakers can gain profound insights into environmental dynamics. These twins can simulate the spread of pollution, model the effects of climate change (e.g., rising sea levels, extreme weather events) on infrastructure and populations, and predict the impact of various interventions. For example, a digital twin of a city’s water network can optimize water distribution, detect leaks, and manage storm runoff more effectively. For climate change research, digital twins can integrate vast datasets from satellite imagery, ground sensors, and climate models to predict future environmental conditions, aid in resource management (e.g., sustainable forestry, precision agriculture), and guide sustainable urban development initiatives, ultimately contributing to a more sustainable planet.
6.4 Human Digital Twins
While still largely in the research phase, the concept of a ‘human digital twin’ is gaining traction, promising a revolution in personalized health and beyond. This involves creating a highly personalized virtual model of an individual, incorporating their unique genetic makeup, physiological data (from wearables, medical records), lifestyle choices, and environmental exposures. Such a twin could revolutionize personalized medicine by simulating drug responses, predicting disease onset, optimizing treatment plans, and guiding preventive healthcare strategies tailored to an individual’s unique biology. Beyond healthcare, the concept could extend to personalized education (simulating learning styles and progress), enhanced athletic performance training, and even highly customized consumer experiences, offering a truly bespoke interaction with the digital world. Ethical considerations around privacy and data ownership will be paramount in this domain.
6.5 Metaverse Integration
Looking further ahead, digital twins are poised to become foundational building blocks for the industrial metaverse. This future iteration of the internet envisions persistent, interconnected 3D virtual worlds where physical assets, processes, and people have their digital twins. This would enable immersive collaboration, remote operations, and enhanced interaction with complex systems. For instance, engineers from different continents could virtually ‘walk through’ a factory’s digital twin, collaborate on design changes, or troubleshoot machinery in real-time, regardless of their physical location. The metaverse would provide a rich, interactive interface for digital twins, making complex data and simulations more accessible and intuitive, transforming how industries design, operate, and innovate.
6.6 Cross-Industry Digital Twins and System-of-Systems Optimization
The current focus largely involves digital twins within specific industries or for individual assets. The future, however, envisions the creation of ‘system-of-systems’ digital twins, where multiple interconnected digital twins from different domains communicate and interact. For example, a digital twin of a smart city could integrate with digital twins of individual buildings, transportation networks, energy grids, and even human digital twins. This interconnectedness would enable holistic optimization, allowing for unprecedented levels of efficiency, resilience, and intelligent management across entire ecosystems, addressing complex societal challenges that transcend individual industry boundaries. This will necessitate advanced interoperability standards and collaborative frameworks.
6.7 Quantum Computing for Enhanced Simulation
In the longer term, the advent of quantum computing holds the potential to dramatically enhance the capabilities of digital twins. The ability of quantum computers to handle exponentially more complex calculations could unlock simulations of unprecedented fidelity and scale, modeling intricate physical phenomena that are currently intractable for classical computers. This could lead to hyper-realistic digital twins capable of predicting behavior with astonishing accuracy, simulating complex molecular interactions for new materials, or optimizing highly correlated systems like global climate models, pushing the boundaries of what digital twins can achieve.
Many thanks to our sponsor Panxora who helped us prepare this research report.
7. Conclusion
Digital twin technology stands as a profound advancement at the intersection of the physical and digital worlds, representing a transformative potential that permeates and reshapes diverse industrial landscapes. By enabling a continuous, real-time mirroring of physical assets, systems, and processes, digital twins empower organizations with capabilities previously unattainable: from hyper-accurate predictive analytics that avert costly disruptions, to granular performance optimization that maximizes efficiency and resource utilization, and to the provision of deeply informed decision-making that fosters agility and strategic foresight. These capabilities collectively enhance operational efficiency, drive sustainable practices, and cultivate a culture of relentless innovation.
However, the journey towards widespread and impactful adoption of digital twin technology is not without its inherent complexities. Addressing critical challenges related to ensuring robust data security and safeguarding privacy, navigating the intricate demands of integration with existing legacy systems, managing the significant capital outlay and achieving demonstrable ROI, and proactively closing the talent gap are paramount. Furthermore, maintaining impeccable data quality and establishing comprehensive data governance frameworks are non-negotiable prerequisites for ensuring the trustworthiness and reliability of these sophisticated virtual replicas.
As technological advancements in artificial intelligence, Internet of Things, cloud computing, and advanced simulation continue to accelerate, the scope and impact of digital twins are anticipated to expand exponentially. Emerging applications in autonomous systems, resilient supply chain management, critical environmental monitoring, and even the visionary concept of human digital twins underscore the technology’s boundless potential. Ultimately, digital twins are poised to redefine how organizations operate, innovate, and interact with the physical world, offering unprecedented opportunities to leverage this powerful and evolving tool to build a more efficient, sustainable, and intelligent future.
Many thanks to our sponsor Panxora who helped us prepare this research report.
References
- time.com: Digital twins used by BMW to reduce planning time by 25% (time.com)
- datanext.ai: General Electric using digital twins for 30% reduction in unplanned downtime for gas turbines (datanext.ai)
- omi.so: Siemens Healthineers developed a digital twin of the human heart (omi.so)
- n-ix.com: GE Healthcare’s ‘Hospital of the Future Simulation Suite’ and Herrenberg, Germany’s urban digital twin (n-ix.com)
- tomorrowdesk.com: Singapore’s ‘Virtual Singapore’ project (tomorrowdesk.com)
- litslink.com: Caterpillar using digital twins for predictive maintenance (litslink.com)
- en.wikipedia.org: Virtual Singapore project details and digital twins in energy management for smart grids (en.wikipedia.org)
Be the first to comment